3D printing with its constantly developing technological possibilities is increasingly reaching various areas of everyday life. Hans Tiismus, who defended his doctorate thesis at TalTech on 2 September, believes that electrical motors will be printed by 3D printers and reach the consumers within the next half a century.
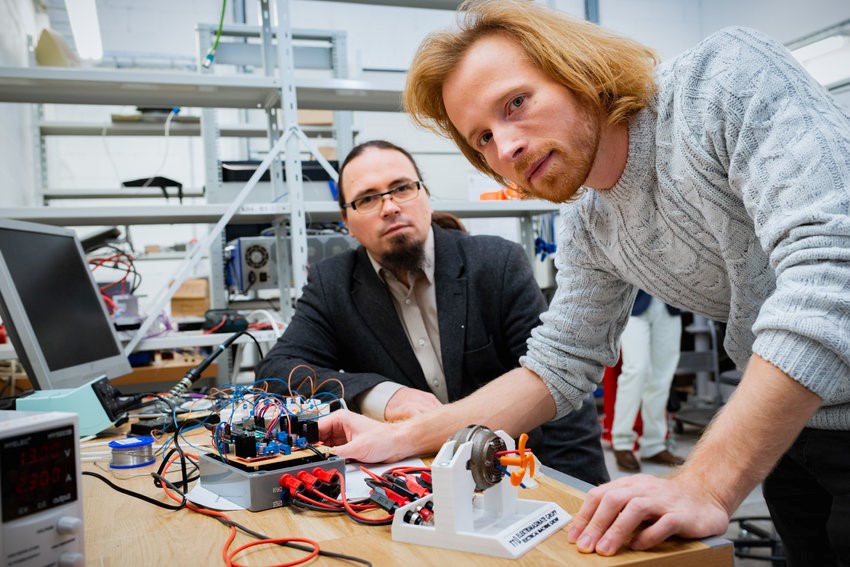
Author: Ain Alvela
In scientific terms, the doctorate thesis of Hans Tiismus, a doctoral student at the School of Engineering of TalTech, focused on developing laser additive manufacturing methods of soft magnetic cores – to put it succinctly, he explored ways to prepare components of electrical motors with a 3D printer. The thesis was supervised by Ants Kallaste and Toomas Vaimann.
Although, the scientist initially mainly focused on laser additive manufacturing of magnetic cores for electrical motors, the long-term goal was to produce an entire motor, whereas it does not matter much when developing the method whether the motor is a small one for powering domestic appliances or a powerful industrial electrical motor – in principle, the technology should be suitable for manufacturing any motor.
Printers must be taught to handle different materials
Currently, the biggest obstacle is the fact that the components of electrical motors, including magnetic cores, are composed of several materials which include metals and non-metals, but the present 3D metal printers are capable of processing only one single-component material at a time. Nevertheless, the scientists managed to complete a fully printed (approximately 50 W) electrical motor with a magnetic core and to compare its characteristics with similar commercial motors. This is the first prototype of its kind in the world.
Actually, they made several prototypes as a number of foreign universities have also shown interest in the topic and further research is going to focus on using the results of their work for calculations for optimising the shape of magnetic and thermal flux as well as electric current conductors.
Ants Kallaste remarks that the goal of the scientific research was not bringing 3D printing to the same level as metallurgical mass production but rather to improve additive manufacturing when producing components with complex shapes in what concerns the precision and range of production. ‘We only have a single-component printer which is best used for printing reluctance rotors that are fairly simple in design. They can be printed in one piece by a 3D printer,’ said Kallaste.
TalTech scientists have already printed stators and transformers as well which means that they have experience in printing the entire magnetic array of an electrical motor and now continue their research to print electrical conductors – windings, etc.
An electrical motor largely comprises three different compositions of materials – magnetic conductors, electrical conductors, and insulation. Hans Tiismus admits that scientists completing something under laboratory conditions unfortunately does not mean that the discovery, invention, or new technology will reach the daily lives of people as a next step. ‘In principle, houses were printed about a hundred years ago but the process was still rather primitive,’ Tiismus said. ‘For printing to become a part of daily life, printing systems and methods for designing the printed items need a developmental leap.’
The speed of the process is no competition for the one of a production line
Ants Kallaste agrees that, in all honesty, 3D printing has still not been properly researched and there is no standard methodology for regulating it, the properties of materials are largely unknown, and for the most part, the necessary tools for solving specific tasks simply do not exist. Until they are created and scientists keep filling in gaps in our knowledge, technologies which have already taken root in everyday life are used in practice.
This does not mean that 3D printing is not developing in leaps and bounds. For example, materials scientists consider all possible composite materials which are available for 3D printing a broad research area.
The first metal printers were created about a decade ago, and now, we can say that these are pretty good at printing a single material. Currently, the Department of Electrical Power Engineering and Mechatronics of TalTech has two 3D metal printers – one can produce components with diameters up to 7 cm and the other one items with diameters up to 28 cm. The researchers dream of the department acquiring a metal printer in the near future, capable of handling several components.
Energy efficiency and material savings are key words in favour of laser additive manufacturing. When assembling normal electrical motors, a large number of various tools, jigs, manual labour, etc. are needed – in contrast, quite a few work stages are skipped with a 3D printer. An engineer only needs to prepare a CAD file which is sent to the printer and the latter will print the object as specified in the file. At the same time, 3D printing cannot compete with a conveyor belt in a factory when it comes to the speed of producing large series of products, as the printers are relatively slow. A component is printed one layer at a time and the thickness of a layer that the laser adds to the item is 50 µm on average. For example, the printer that the researchers used took about 72 hours for printing the magnetic cores of the first prototype of a 50 W motor when conducting research for this doctorate thesis.
The efficiency of printed motors needs improvement
The efficiency of electric motors largely depends on two types of losses – hysteresis and eddy current losses. The first one is determined by the properties of the magnetic material of the machine, the second one is due to magnetic material conducting electricity. In regular electrical motors, isolated electrical steel is used for reducing eddy current losses. When only printing electrical steel without an insulating material, we get a monolithic magnetic core, leading to large eddy current losses.
‘We must find a solution for reducing eddy current losses; unfortunately, there is no good technology for this at present,’ admit the researchers. ‘We have relied on cellular structures which allowed reducing the losses somewhat. This means that we printed empty cells within the core. This technology needs to be developed further. As the eddy current losses of our machines are already larger than normal, they are not yet capable of competing with regular electrical motors in common use. They are not as efficient as regular motors, which is why we do not consider our motor completed yet.’
In numbers, it can be expressed as follows – if the efficiency of a commercial 50 W electrical motor is 52%, then the efficiency of the motor printed at the TalTech laboratory is about 34%. In the case of transformers, these figures are 80% and 70% respectively. At the same time, these are admittedly the first prototypes of their kind in the world.
‘We are continuing to develop the structure and materials of printed cores and it is very likely that we will catch up with machines produced in traditional ways soon,’ Hans Tiismus promises.
Both Kallaste and Tiismus believe that 3D printing is unlikely to be able to compete with the mass production of electrical motors; however, it could help when integrating motors with required qualities to specific systems in the future.
3D printing can be used to create unique products
‘Printing technology could be competitive in project production. It could be used to produce machines which are integrated into systems, meaning that a completed machine is not purchased from a shop and then fitted for the system; instead, the necessary machine is designed for the system along with its external shape, its contents, and characteristics according to requirements,’ Kallaste describes the possible future of 3D electrical motors. ‘The motor could be for anything, such as a drone, a manual tool, or a piece of space equipment.’
‘The goal is to optimise the motor to the point where a 3D printed motor is better and more suitable for a specific function than a regular motor,’ Tiismus adds. ‘It might be a lot more expensive than a normal motor, but in these instances, the price is usually a secondary concern to the motor fitting the system.’
Kallaste believes that a manufacturing company having a concrete interest in this field would really help the research. He notes that it would help the scientists focus their activities on solving a distinct problem or fulfilling a specific task. Otherwise, academia might become too theoretical in its work; the participation of a manufacturing company would help scientists target their research to find tangible practical solutions. After all, research community toils so that the results of their work, even if only a few, would reach production and be used by humankind.
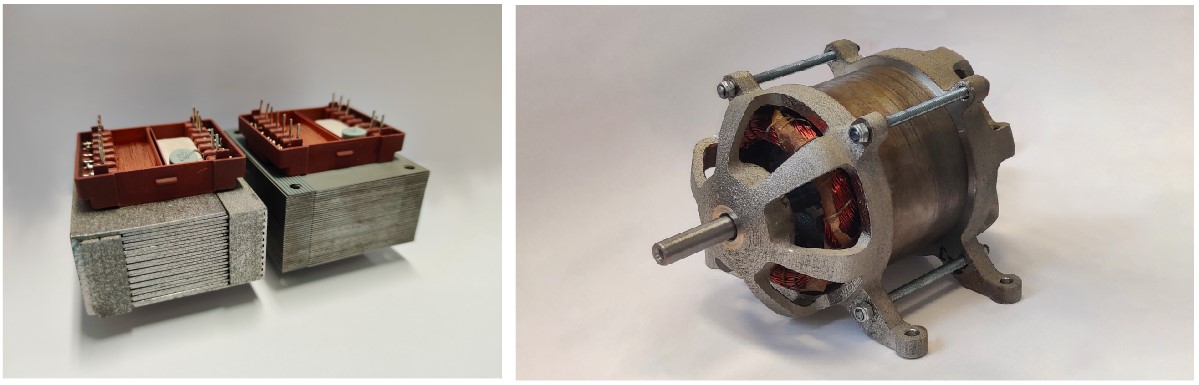
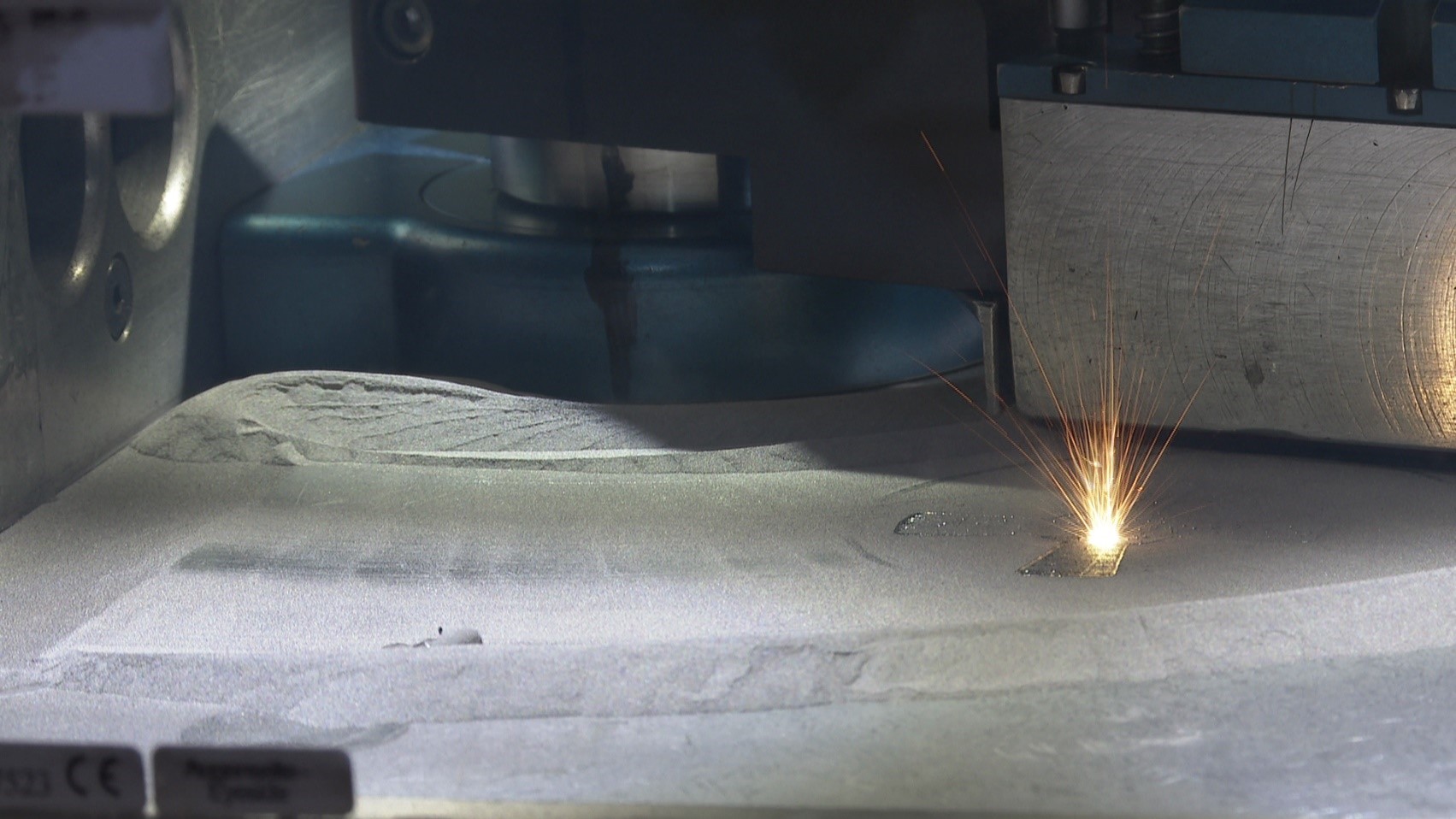