In cooperation with the engineers of Tallinn University of Technology and the rehabilitation team of East Tallinn Central Hospital (ITK), 3D-printed orthoses are being developed.The orthoses are recommended by a doctor, and made in accordance with the patient's body shape.
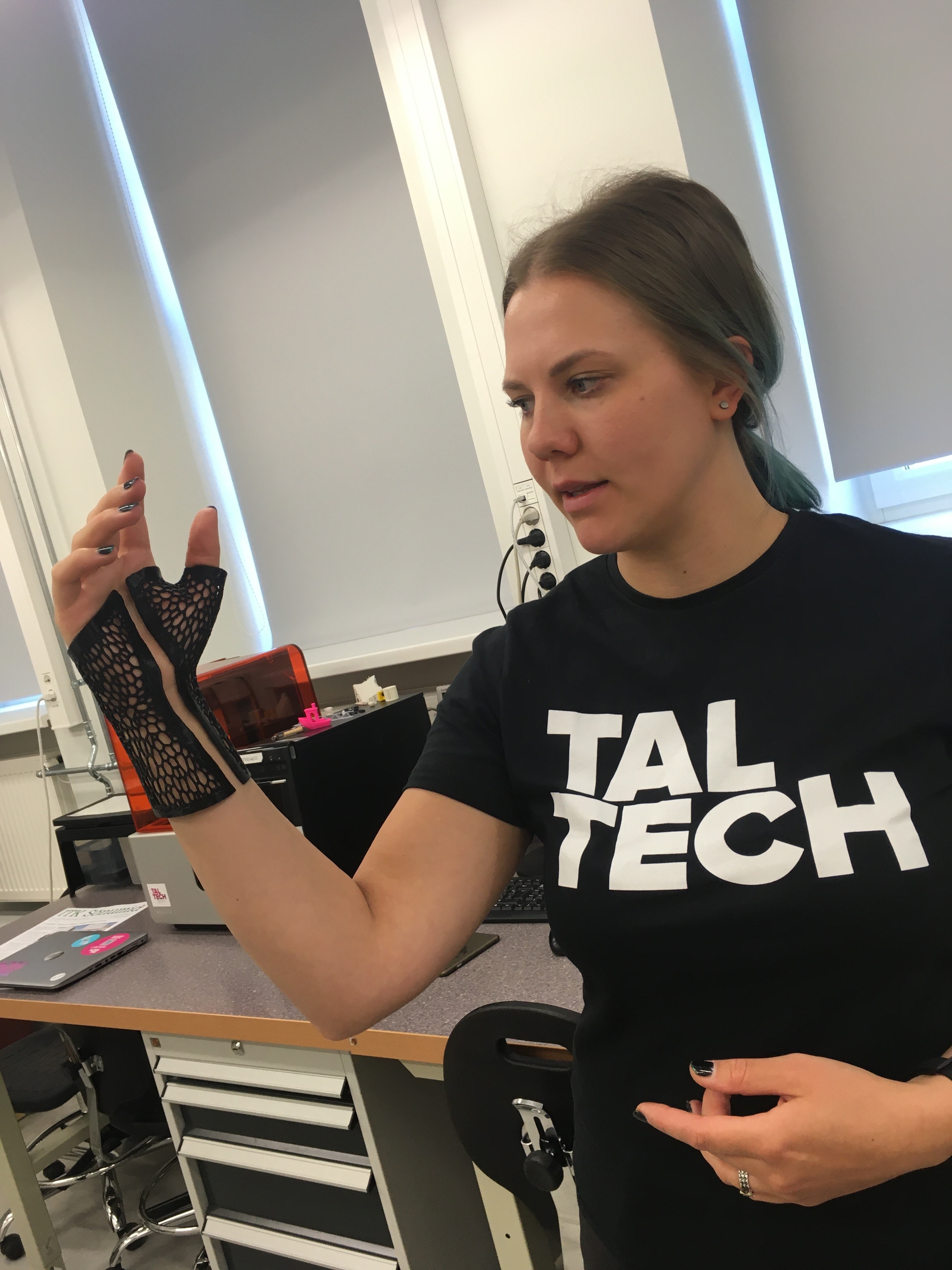
According to Tauno Otto, an engineering scientist at TalTech, the next stage in the research and development process is the sensors that will monitor the wearing time and use of the orthosis.These sensors work as an input for artificial-intelligence-based mobile and PC applications that suggest medical exercises to the patient.
Geithy Sepp, a doctoral student at the Faculty of Engineering and a development engineer at East Tallinn Central Hospital, thinks that future developments will be focused on adding sensors to the orthoses of scoliosis (a sideways curvature of the spine), as the wearing time significantly affects the outcome of the treatment. The sensor lets the doctor know when and for how long the back support has been worn, which makes it easier to evaluate the effectiveness of the treatment.
Another innovation would involve the participation of GPs in the process of orthosis printing in the future. Dr. Heidi Alasepp, Head of the Clinic of Medical Rehabilitation of East Tallinn Central Hospital (ITK), explains: "If a patient needs an orthosis in, for instance, Rapla, a GP or a nurse can make a 3D scan of the limb and send it to our development centre, where it will be designed and printed."
Currently, 3D printed orthoses are still in the research and development stage. To make them accessible to people, the whole process needs to be made smarter and more automated, following the regulations of medical devices at the same time.
Heidi Alasepp said that developing the ability to print individual 3D orthoses is a significant and steady step forward in personal medicine. "The goal is to improve people’s health and quality of life," Alasepp added.
The young researchers of TalTech, and the specialists of ITK, are currently focusing on support tools for the hands and back. These unique and aesthetically pleasing orthoses are made in accordance with the condition and measurements of the patient.
Geithy Sepp believes that the process begins with the doctor diagnosing the patient and assigning them the corresponding orthosis. For example, a patient with arthritis may be prescribed wrist support. The engineer then makes a 3D scan of the hand and 3D-models the orthosis, which is later printed out. Printing takes 2–10 hours depending on the size of the orthosis.
“The digitalisation of the production makes the process more convenient for both the manufacturer and the patient,” doctoral student Sepp explained. “What is more, 3D printing makes it possible to produce designs with complex and combined functionality that would be too expensive or even impossible to produce using conventional methods.”
One of the greatest advantages of these orthoses is the innovative perforated structure that lets the skin breathe during hot summer weather.
In addition to the medical qualities, the colour and comfort of the supports are also important, the orthosis manufacturers say. “Children enjoy wearing the orthosis more when it is colourful or has a playful image on it. And when the patient is happy with the orthosis they are more eager to wear it,” Sepp explained.
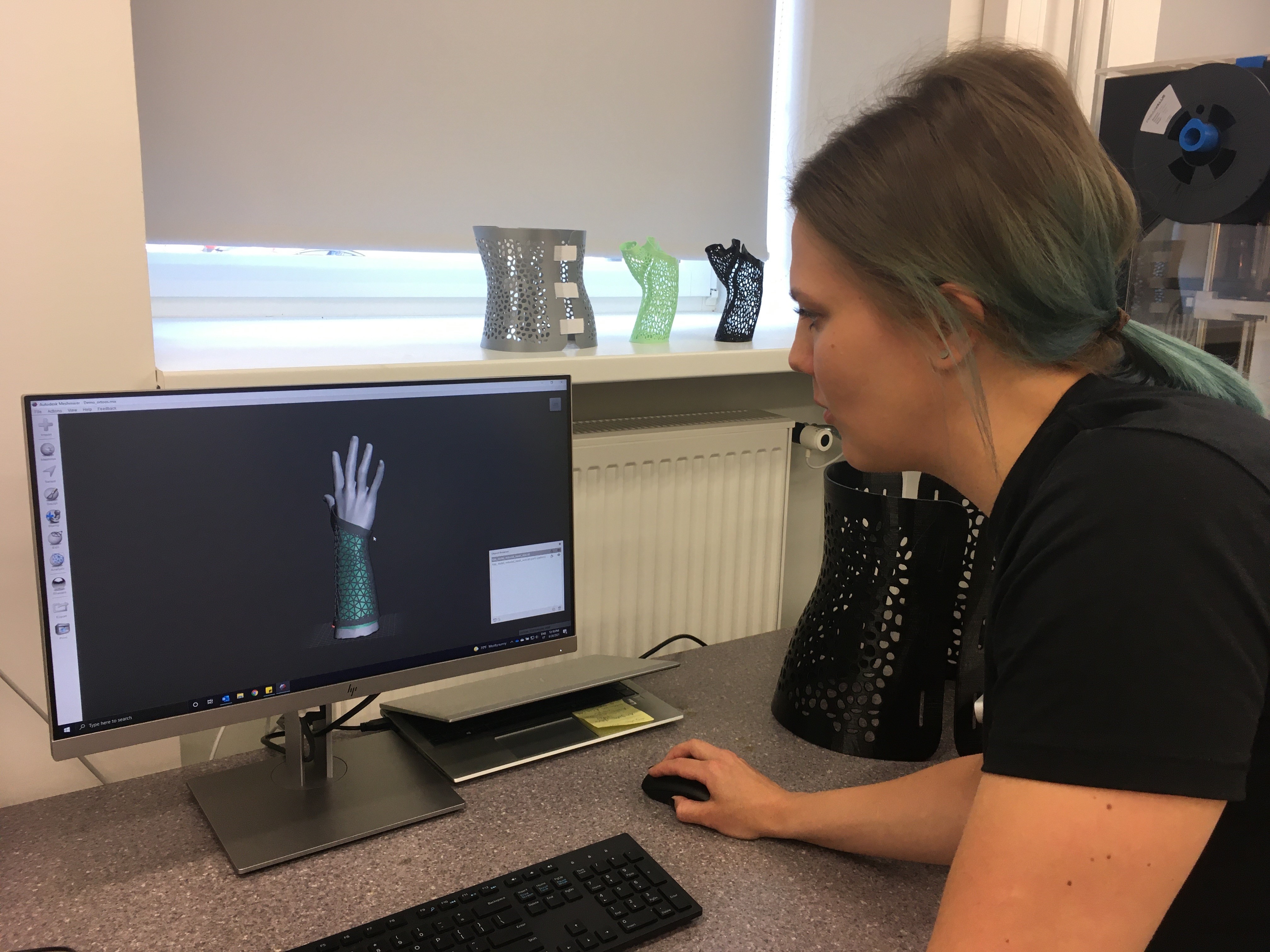