Every day, thousands of tons of eggshells are thrown away that could be reused in orthopedic bio-implants. This would help to promote the circular economy and reduce environmental impacts, according to the research of Riddhi Hirenkumar Shukla, PhD candidate at Tallinn University of Technology.
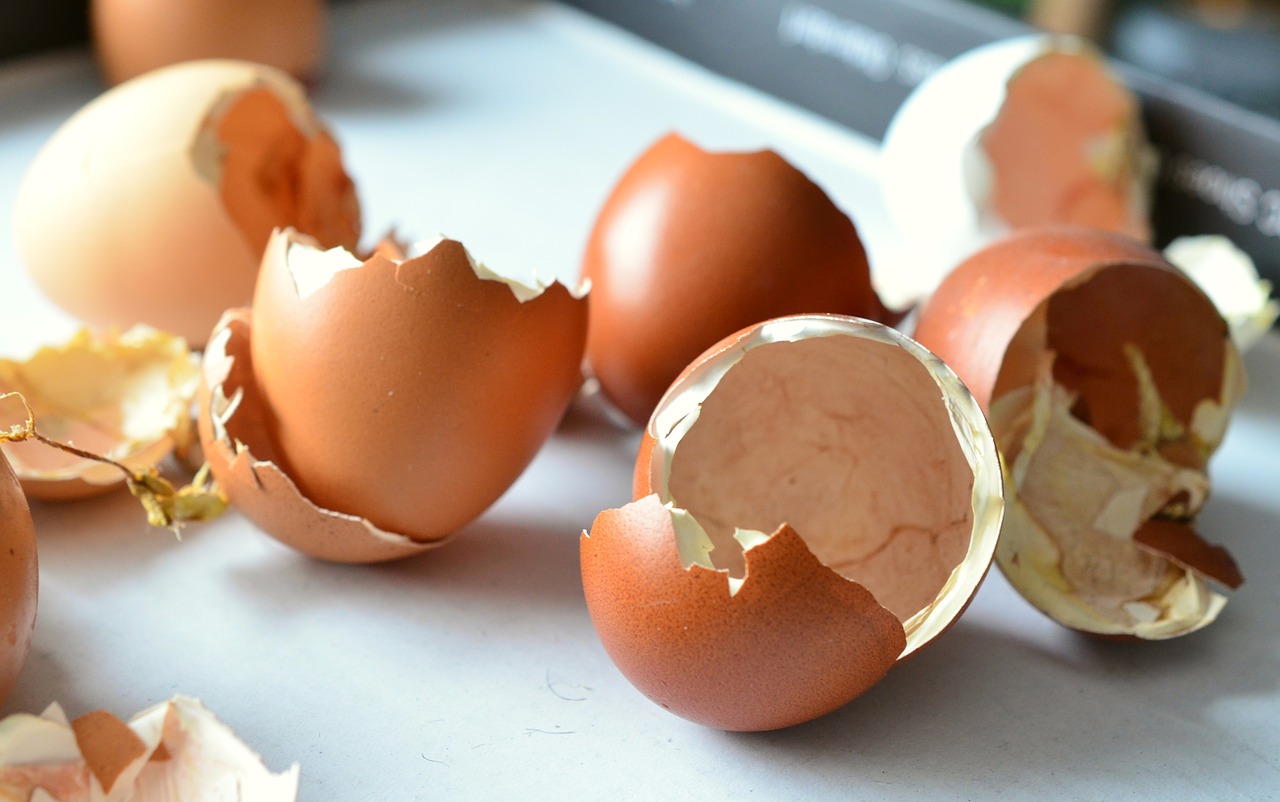
Eggs are a common food ingredient found in daily diets. The inner core of the egg and the thin protein layer (albumin) are useful for food processing, while 11% of the egg is made up of a ceramic shell (eggshell) without any attempt to give it a further value. In the best case, they end up crushed in the chickens' diet to cover their calcium needs. However, a large portion is simply thrown away. Approximately 2,000 tons of eggshells are discarded daily.
At the same time, they are rich in several important elements. Eggshells are primarily composed of calcium carbonate, along with various other calcium compounds and trace elements such as Na, K, Mg, and Sr. Remarkably, natural bone also contains similar amounts of calcium carbonate and these trace elements in similar quantities. “The disposal of eggshells not only results in the loss of these valuable elements but also poses significant waste management issues,” Shukla stated.
Dumping eggshells can foster the growth of bacteria and fungi, which have the potential to cause diseases. “Moreover, landfill disposal costs money, and the decomposition of organic matter from eggshells produces foul-smelling gases like ammonia, methane, and hydrogen sulphide. Microbial action on the eggshells further contributes to environmental concerns,” said the researcher.
A new life for eggshells
Despite many efforts to utilize eggshell waste, it remains a major issue. “My research aims to repurpose eggshell waste for use in orthopedic bio-implants, promoting sustainable production through a circular economy and reducing environmental impact” noted Riddhi Hirenkumar Shukla. However, the idea currently has its own problems.
While eggshell-based bio-implants are promising, their brittle nature poses challenges in load-bearing implants such as knee or hip replacements. “To address this, we have introduced hierarchically porous titanium (Ti) into the eggshell implants,” said Shukla. He added that the porous titanium was produced using a cutting-edge additive manufacturing technique, where the sample is built layer by layer, joining metal powders. These layers are as thin as 30-50 microns, allowing for the production of complex geometries without material waste. Even more impressively, this technique is so advanced that it can produce bespoke bone designs tailored to individual patients. But it doesn’t stop there—you can manufacture patient-specific implants in a single batch, making personalized medicine more efficient and accessible. After constructing the titanium structure, the pores are filled with eggshells using spark plasma sintering, another advanced technology. In the experiments, the researchers sintered the eggshell powder at six different temperatures, from 250 °C to 1000 °C. As a result of the analysis, they found that the best density and hardness were obtained when the spark plasma sintering temperature was 850 °C. “The combination of these two materials is crucial, as the porous titanium provides structural strength, while the eggshell enhances bioactivity” explained Shukla.
Bioactivity refers to the ability of the artificial implant to integrate with natural bone. “Titanium and other metal-based bio-implants are common, but they are bio-inert, meaning they do not easily integrate with natural bone. Additionally, if these implants become infected during surgery, they can harbor bacteria, leading to detrimental consequences. In some cases, patients require long-term antibacterial medication” said the researcher.
The bio-inertness and risk of bacterial infection often lead to revision surgeries, which are painful and costly. This is where the Ti-eggshell composite bio-implant produced through this method by the TalTech researchers could come to the rescue.
The study is available in the Journal of Alloys and Compounds. The other authors of the research article are TalTech Professor and supervisor of this research work Konda Gokuldoss Prashanth and Rathinavelu Sokkalingam from Sweden's Karlstad University.
This article is based on the news article published by Novaator.