Electrical Machines Research Group
Electrical Machine Group (EMG) is a research group within the Department of Electrical Power Engineering and Mechatronics in TalTech, Estonia, specialized in electrical machines and drives.
The group carries out R&D as well as study programs in the fields of interest and consists of various specialists of this scientific area.
ELECTRICAL MACHINES RESEARCH GROUP ROLL-UP

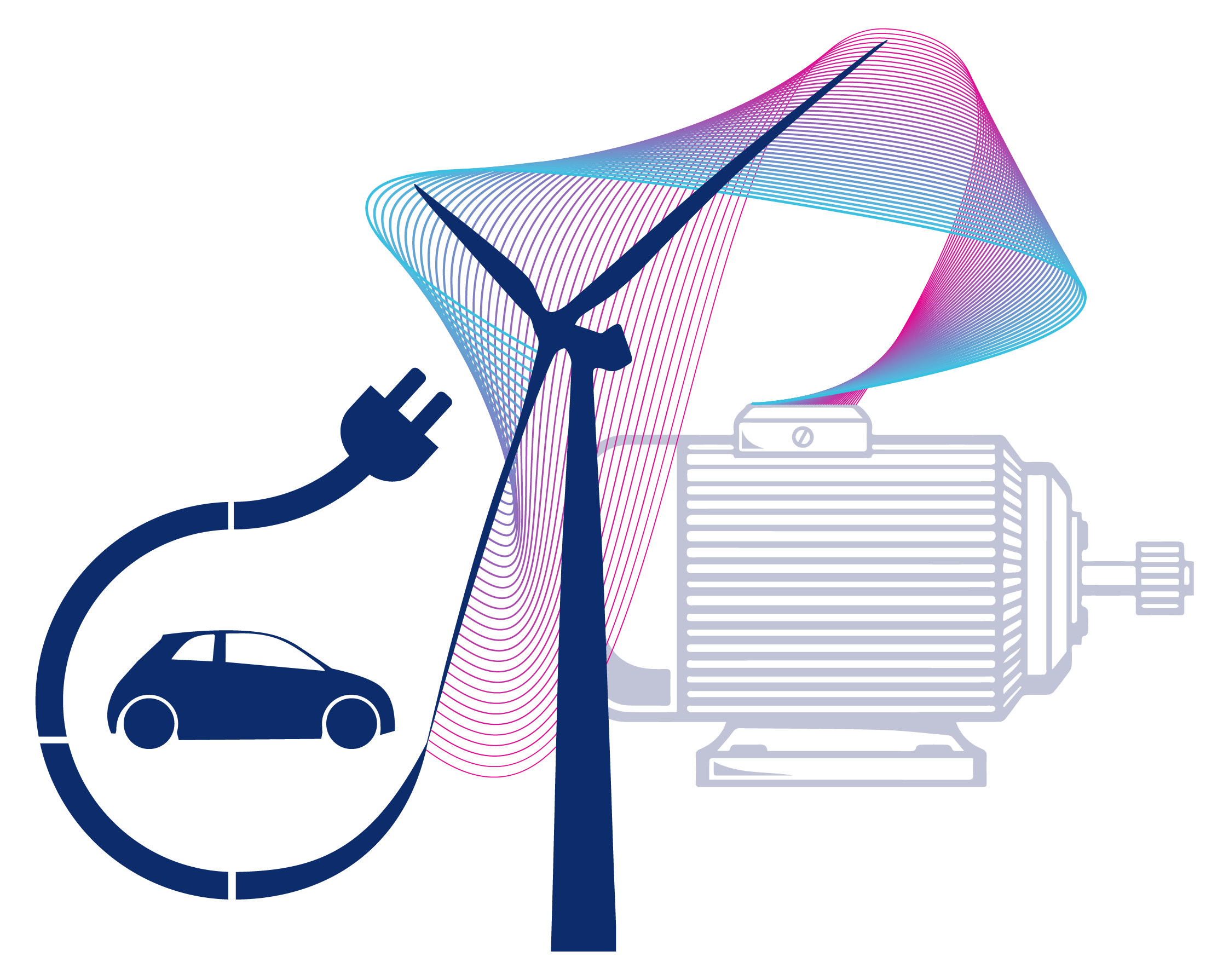
![]() Tenured Associate Professor | ||
![]() | ![]() | ![]() |
![]() | ![]() | |
![]() | ![]() | ![]() |
![]() Early Stage Researcher |
Slow-speed permanent magnet synchronous generators for wind applications
The research in the field has been carried out during more than 10 years. R&D has been carried out mainly for low and medium power radial flux machines (1-150 kVA). Both inner and outer rotor construction using different magnetic materials (NdFeB, SmCo, ferrite) have been investigated. Knowhow of this research field has been utilized in the development a 3 MVA ring-shaped generator used in wind turbines. Further studies of this field are also dedicated to the investigation of high speed (6000 rpm) permanent magnet machines that can be used as generators or motors in Unmanned Aerial Vehicles (UAVs).
Diagnostics of electrical machines
The investigation towards the prediction and diagnosis of different electrical machine faults is been carried out in the EMG. Mainly induction machine rotor and stator faults (broken bars, eccentricity, stator short-circuits) have been the subject of the study. Some attention have been paid also to the diagnostics of faults in synchronous machines.
Novel approaches to electrical machine fault diagnosis
Along with the more traditional diagnostic approaches, several novel and emerging technologies in the field are being investigated. Some of the approaches involved are:
- Usage of mobile phones and other similar devices for simple pre-diagnostics of electrical machines,
- Usage of cloud computing environments and IoT (Internet of Things) solutions for diagnostics in the view of Industry 4.0,
- Implementation of inverse problem theory in the field of electrical machine diagnostics to further enhance the early stage recognition of the faults and improve the overall precision of detection.
Novel permanent magnet materials for the use in sustainable energy applications
The aim of the research is to design materials with comparable or even better magnetic properties to materials commercially available today but with reduced cost and impact on the environment. The main topics of the research include development permanent magnet alloys with controlled composition and microstructure; development of magnets with improved performance at high operation temperatures (up to 150°C); prototyping of several new grades of permanent magnets with reduced content of Nd and Dy providing alternatives to those of manufactured by conventional compositions and methods.
Research of novel permanent magnet materials is being carried out in cooperation with the department of material technology in TTÜ and several industrial partners. The main task for EMG in this research is the design of new materials and grades for wind generators, assessment and specification of the material properties etc.
Design and optimization of electrical machines and drives
In this research building of novel optimization procedure, which accounts for the whole life-cycle of the motor-drive and includes the different phases of the ecodesign and their environmental impacts is proposed. Such a procedure will result in life-cycle energy and resource efficient designs and contribute to the protection of environment. The research itself includes building of different simulation tools, survey among the stakeholders and extensive use of distributed computation to achieve a sustainable design of a selected range and type of motor-drives. The practical implementation of the developed design and optimization methodology will be realized on 10 kVA permanent magnet assisted synchronous reluctance machine.
ISEAUTO: Estonian first self-driving car
EMG in cooperation with mechanical department of TTÜ and industrial partners working together to design and build a self-driving car. The main goal of ISEAUTO project is to develop a fully self-driving vehicle that is going to drive around the university campus and will be a research and educational platform for students, researchers and even entrepreneurs.
EMG is responsible for the electronic part of ISEAUTO and developing of the autonomous charging station. The electronic part includes wiring, placement of sensors and actuators, tuning and testing of traction drive system of ISEAUTO. The autonomous charging station will provide the possibility to charge the car without human interaction. It will incorporate the machine vision and communication parts.
Additive Manufacturing of Electrical Machines
Additive manufacturing, also known as 3D printing, is opening up new ground for innovations in low-volume production due to faster and cheaper prototyping, reduced lead time and shorter supply chains. It is a relatively new technology, which enables the tool-free production of components and entire assemblies directly from a CAD file. Today, the technology is still not widely used in industrial production, but it is gaining more and more popularity. There is a need for principles how to design electrical machine so that it would be suitable for 3D printing.
The main objective of the project is to develop a design methodology for 3D printed electrical machines, which would be able to compete with the conventional machines manufacturing method.
Lifecycle assessment of electrical machines
Project target is an electrical machines for wind turbine applications. Wind energy is the most cost-effective climate change mitigation technology. The main goal of the project is to perform Life Cycle Analysis to determinate a quantity of raw materials of different electrical machines used for wind applications. The lifecycle assessment implies important procedures that can help reduce electrical machine impact on the environment, thus being an instrument for assessment of the influence exerted by particular products on the environment – from cradle to grave – beginning with acquisition of the materials followed by manufacturing, transporting, marketing, use and recycling.
In hand with optimized predictive maintenance and condition monitoring approaches, it helps to lower the price of renewable energy generation, empowering the further alternative energy use instead of burning fossil fuels.
Subjects for PhD thesis
Note, that those are just keynote topics. The final research objectives will depend on qualification of PhD student and research group needs. Please don't hesitate to contact us.
ELECTROMAGNETIC DESIGN OF SYNCHRONOUS RELUCTANCE MOTOR
The main tasks of the thesis are:
Within this thesis, the PhD candidate will learn about the design and optimization of special types of electrical machines. We will provide the necessary software for the numerical analysis of the machine but the candidate will be responsible for developing and implementing the optimization procedure. At the end of the thesis, a prototype machine will be built and the candidate can participate in this process too. The main tasks of the thesis are:
- Primary design of the machine without magnets. A synchronous reluctance machine, without permanent magnet, will be designed. The rotor flux barriers and the windings as well as the geometry of the stator will be the starting point
- Secondary design with ferrite magnets (power factor). The power factor of synchronous reluctance machines is known to be low. Improving this power factor can be achieved by additional permanent magnet in the rotor of the machine. The design of this so-called pm-assist machine is challenging and need some computations.
- Geometrical optimization. After the two machines have been designed, the candidate will have to optimize the machines through numerical analysis and optimization procedure. The optimization targets are the torque, the torque ripple, and the efficiency.
- Material optimization. The geometrical optimization does not account for the material and other cost. To make the machine attractive for industry applications, the manufacturing and material cost has to be accounted for in a hypothetical series production process. This optimization can be achieved if materials databases are available and manufacturing details are explicit. The optimization could be carried out as a multi-objective task.
Within the PhD studies, the candidate will present his/her work in international conferences (funded by the project) and publish journal papers required to complete the thesis.
Contact information:
The theses will be carried out under the supervision of Prof. Anouar Belahcen and Dr. Ants Kallaste. The theses are part of a large research project funded by the Estonian Ministry of Education and Research.
DEVELOPMENT OF CONTROL METHODS FOR SYNCHRONOUS RELUCTANCE MOTOR/h4>
The main tasks of the thesis are:
Within this thesis, the PhD candidate will learn about the control and application of special types of electrical machines. We will provide the necessary hardware and software for the real-time control of the machine but the candidate will be responsible for developing and implementing the control algorithm. The main tasks of the thesis are:
- Design of loss reduction control algorithms for - Usually the optimization concerns only the motor losses, whereas the converter losses are often neglected. Effective loss reduction strategy will require to consider motor and converter losses. Achieving this objective for the novel permanent magnet assisted reluctance machine could help to improve existing control strategies.
- Real-time simulation. - Design control algorithms, vision, or plant model in MATLAB/SIMULINK. -Build a real-time application from MATLAB/SIMULINK to the target machine. -Set-up and tune signal parameters from within MATLAB/SIMULINK during real-time execution
- Practical tests on the test bench. The test bench, combining advantages of real-time software models and real equipment, contributes to the reduction of the number of test runs and safe maintenance. Test benches cover many different areas like energy management, optimal configuration, combination of different energy sources, etc. Research goals will be achieved by proper verification of the model.
Within the PhD studies, the candidate will present his/her work in international conferences (funded by the project) and publish journal papers required to complete the thesis.
Contact information:
The theses will be carried out under the supervision of Dr. Anton Rassõlkin and Dr. Toomas Vaimann. The theses are part of a large research project funded by the Estonian Ministry of Education and Research.
IMPLEMENTATION POSSIBILITIES FOR INVERSE PROBLEM THEORY IN FAULT DETECTION OF ELECTRICAL MACHINES
possible to detect the faults in such stage, when repairing of the machines is still possible or reasonable.
In the usual diagnosis problems, the emphasis is put on the signal processing in view of extracting useful data from the global quantities, usually the machine current. If more information about the fault is needed, a physical model of the machine is usually constructed and the fault is simulated to extract the local data. This is a forward problem, where the cause is the fault and the consequences are the distortions in the local quantities. The effect of these distortions on the global quantities is usually also sought from these forward simulations through either analytical or experimental procedure.
In the proposed thesis, physical models of the electrical machines based on their numerical analysis (Finite Element Method) are to be develop and then used to derive an inverse problem and solve it. The inverse problem consists of the reconstruction of the local quantities from the global ones. It is however clear that this problem is ill-posed in the sense that it has more than one solution. The essence of the thesis is thus to find out how to deal with this ill-posed problem and find enough global information to solve it.
Within this thesis, the PhD candidate will learn about the diagnostics and fault detection of electrical machines. At the end of the thesis, a novel approach for implementing inverse problem theory in the diagnostics of electrical machines will be developed.
The main tasks of the thesis are:
- Inverse problem theory. A comprehensive theoretical background of inverse problem theory and implementation possibilities in fault detection of electrical machines
- Physical model of the machine. A number of different fault types and severity levels can be chosen to be used for further analysis. Finite element model of an induction machine that can be used in the solution of the inverse problem will be built
- Inverse problem model. Strategies to solve the inverse problem. Finally finding a working strategy to solve the inverse problem even in case it is ill-posed
- Signal processing and verification. A signal analysis method altogether with the quantities to be analyzed. Verified reconstruction of the local quantities from the global ones
Within the PhD studies, the candidate will present his/her work in international conferences (funded by the project) and publish journal papers required to complete the thesis.
Contact information:
The theses will be carried out under the supervision of Prof. Anouar Belahcen (anouar.belahcen@aalto.fi) and Dr. Toomas Vaimann. The theses are part of a large research project funded by the Estonian Ministry of Education and Research.
- analysis, design, optimization and development of electrical&; machines (including wind generators)
- magnetic field calculations, simulations and measurement
- permanent magnet applications and implementation studies
- novel methodologies for design and optimization of electrical drives
LABORATORY SERVICES
- monitoring of the cooling conditions of electric machines in a wind tunnel
- diagnostics and testing of electrical machines
Contact:
Toomas VAIMANN
toomas.vaimann@taltech.ee
6203800
Electrical Machine Group is located in the TalTech campus in Tallinn, Estonia. There are a fully equipped electrical machines study laboratory and scientific laboratory for the use of the group. Scientific laboratory of electrical machines is in a continuous development. Currently, electrical machines in the power range of 45-50 kW can be tested in the facilities. Thermal conditions of the machines can also be monitored and cooling tests of wind generators can be performed using a wind tunnel. Experimental assessment of losses and thermal processes of electrical machines are also possible to perform. There is a full setup for different electrical machines diagnostic tests with a large number of same series machines as well as converters and possibility of inflicting almost any electromechanic fault. All of the measurements can be recorded simultaneously and control algorithms can be tested using special build converters and real time target machine.
Scientific partners
The scientific cooperation network of Electrical Machine Group consists of, but is not limited to, universities and research institutions of Estonia, Finland, Latvia, Sweden, Czech Republic and other countries. Group is actively broadening the international cooperation network and searching for new partners in the field of electrical machines and drives.
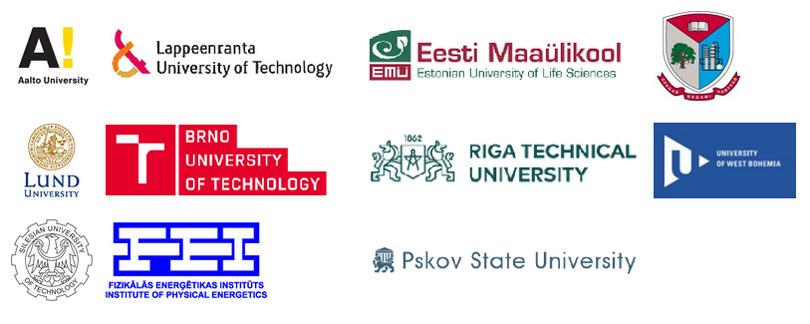
Industrial partners
There are numerous international and domestic companies with whom the Electrical Machine Group is cooperating. The most known of them include:
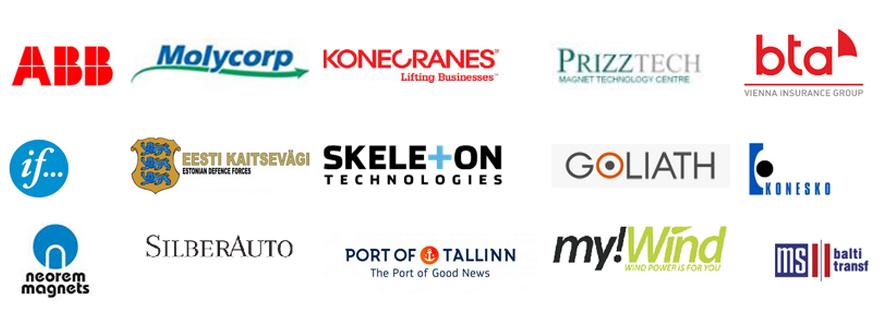
Skype EMG_TUT
EMG@live.ttu.ee
Facebook
Linkedin