The main objective is to develop autonomous, self-driving mobile robots which are focused on automating the transportation and delivery tasks by autonomously transporting and delivering materials and products.
The wider vision and objective of autonomous vehicle research and devel- opment is to introduce a small scale future city environment into university campus, where autonomous vehicles are in the focus. Whether these vehicles are small package transfer robots, mid-size autonomous agricultural vehi- cles or full scale self-driving cars, the main research activity in autonomous systems lab is a full development of a Last Mile type vehicle in cooperation with a private company. As a result of the one-year development project, a self-driving car will be prepared, which started driving in the campus of Taltech in 2018. The vehicle is fully autonomous and is built on open source software solutions.
Read more on this page.
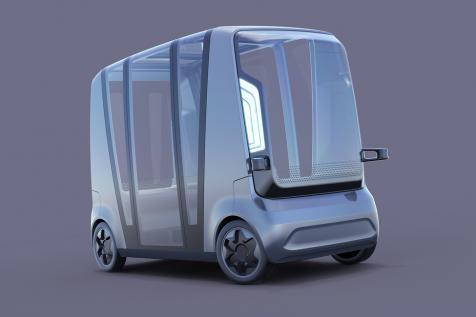
The objectives of the development, in addition to research, are the following:
• Future city research and development platform. We are offering a service platform for students and companies where they can use a self-driving car and other smart infrastructure components for developing new and innovative services.
• Knowledge and competence. One of the goals of the project is to develop competence and know-how at the university level about self-driv- ing cars. As there are many students involved, we provide valuable practical experience to future engineers in Estonia. The project gives also a signal for students that modern education is provided at TalTech and students can engage in practical studies in an area of interest.
Head of research group:
Raivo Sell
raivo.sell@taltech.ee
The process of grinding into powder is both the beginning and the end of the lifecycle of almost any product created by men. As tens of thousands of years ago ancient men ground paints and grains in a mortar, modern men use the method of grinding into powder for a large variety of materials. The needs of humanity in this regard continue to grow.
Grinding processes are required to manufacture new products or produce raw materials for them, as well as for recycling and reuse. The problem of recycling and reuse of materials is becoming more relevant than ever before.
The combined systems of impact grinding and separation based on disintegrator mills were developed at TalTech (Tallinn University of Technology) operating at different modes of grinding ( direct, separative and selective grinding, as well proportional and steady grinding).
Unlike the traditional grinding methods, disintegration breaks up the material by a series of high-speed impacts, which generate stress within the material particle tens of times greater than its strength. Combined with a built-in inertial separation system (Fig.1) it makes possible to produce powders of materials that are generally considered impossible to obtain using such types of mills (for example plastics, rubber, hardmetals, composites etc.)
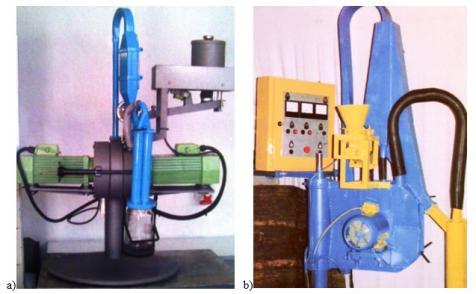
Fig. 1 Laboratory disintegrator milling system DSL-175(a) and semi-industrial disintegrator mill DSL 115 (b) with the inertial–centrifugal air classifier
The processes accompanying disintegration also greatly alter the mechanical and chemical properties of the material. When the particles are rapidly destroyed, surface oxide films are torn off, microclods are broken, and a large amount of new unoxidized surface is formed, which has extremely high chemical reactivity. The spatial pattern of the grains of the material is distorted, numerous defects emerge, and so mechanochemical processes are taking place not only on the freshly formed surfaces but also in the volume of ground crystals.
The main activities of the laboratory of disintegrator technology are connected with the development of disintegrator milling systems for processing of different materials and applications of recycled materials for development of new products (see Fig.2).
Based on the disintegrator milling technology, grindability of different groups of materials was studied:
• metallic materials: cast iron and non-iron alloys chips, stainless steel and Ni- and Co- based alloys (examples of ductile material),
• ceramic materials: mineral ores (examples of brittle materials),
• composite materials: hardmetal (example of hard composite material), plastic composites, printed circuit boards (example of metallic-GFRP laminated plastic composite) and automobile tire covers.
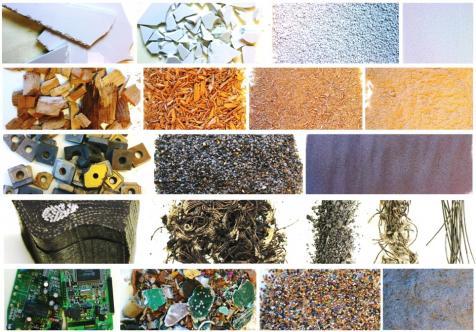
Fig.2 Examples of disintegrator-milled materials for reuse.
Head of research:
Dmitri Goljandin
dmitri.goljandin@taltech.ee
The main objective of the research is to study and develop a Production Monitoring System (PMS) with Predictive functionality that operates in near real time, focusing on SMEs. The main activities of the research are: development of PMS concept; system prototyping; model predictive control development.
Production monitoring information can be classified into two major groups: the status of resources and the status of jobs. The status of jobs is related to processing time, production sequences, etc. This overview of the production processes supports planning and scheduling. The status of resources is related to the information concerning machinery, material and labour. Machinery is monitored to get the data about the tool wear and to provide information on the state of the tool or component and availability of machinery. The status of every machine or production line is evaluated by Key Performance Indicators (KPI).
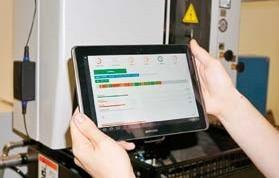
Developed real-time production monitoring system and black sensor box in manufacturing unit.
The advanced Production Monitoring and Prediction System is detecting, mea- suring and monitoring the variables, events and situations which affect the performance and reliability of manufacturing systems and processes. Efficient, real-time feed of information for production control and monitoring includes data acquisition about state of equipment, production orders, flow of materials, quality of products, process data and other necessary data which are used for making the proper and optimised decisions, regarding manufacturing planning, improved use of available resources, planning of equipment maintenance etc. The two stage tool life expectancy model based on derivation of the discrete analytical tool life prediction model and artificial neural networks model for determining dependence of the vibrations, temperature and cur- rent on process parameters (cutting speed, feed rate and cutting depth) was developed and tested. The proposed concept and predictive model allows estimation of the remaining tool/component life also for a partially used tool based on the values of processing parameters, working regimes, etc. during
used and future exploitation time.
Development of an advanced Production Monitoring and Prediction System is a continuous process and with regard to diversification there is definitely a need for more case studies and different developments.
Head of research group:
Kristo Karjust
kristo.karjust@taltech.ee
Development of new advanced materials in particular powder metallurgy (PM) materials and related technologies is one of the major factors for industrial success. Combination of desirable properties of advanced PM materials is met in multiphase material structures including ceramic-metal composites - cermets and cemented carbides ( hardmetals). One of the promising fields of cermets application is their use in tribological application where resistance to monotonic and cyclic loading and corrosion becomes an important factor to improve durability of tools and wear resistant parts.
The research in the field of wear resistant composites (tribocomposites ) of enhanced mechanical and corrosion reliability produced by advanced PM manufacturing methods has been carried out in TTÜ for many decades. Latest research has been focused on development of tribocomposites for a wide range of temperatures, characterization of these composites based on carbides, carbonitrides, nitrides and establishment of the generic relationships between materials performance, structure and processing route. The aim is development and/or optimization of ceramic-metal composites of high hardness and strength, enhanced fracture toughness and excellent wear or corrosive-wear resistance that is sustainable in a wide range of temperatures. The research program is mostly focused on titanium carbide, carbonitride, nitride ( TiC, TiCN, TiN ), chromium carbide ( Cr3C2 ) and tungsten carbide ( WC ) based composites
Examples of the latest research activities and results for industrial applications are as follows:
- Development and use of ceramic-metal composites ( cermets and hardmetals ) as tool materials for friction stir welding (FSW) of aluminium alloys and low-carbon steels. It has been revealed that prevailing degradation mechanism of tools during FSW is adhesion. It has been also established that WC-Co hardmetals and TiC-Fe alloy ( steel ) cermets compare favourably with other ceramic –metal composites in adhesive wear conditions.
- • Development of Ni- and Co-free ceramic-metal composites ̶ TiC-, TiN- and Cr3C2-based cermets and WC-based cemented carbides. Iron based binders binders with different structure are used to replace toxic metals (Ni, Co) in these composites. The focus of research is at present prevalently on utilisation of Ni- and Co-free high-chromium corrosion resistant ferritic steels as alternative metallic binders. The phase transformations and microstructural evolution ( see Figures 1 and 2 ) ) during sintering as well as mechanical and corrosion behaviour of these composites have been revealed.
- • Investigation of contact fatigue behaviour of ceramic-metal composites on basis of TiC, Cr3C2 and WC of different composition produced using different technological routes ( vacuum sintering, Sinter/HIP, reactive sintering , spark plasma sintering ( SPS ) ). Contact loads of cyclic nature between contacting surfaces are common e.g. in cold forming tools and machine components. The mechanical response and the damage mechanism during contact fatigue have been disclosed.
- • Development of reliable technology of induction air brazing of titanium carbide- based cermets to steels using commercially available Ag – and Cu- based filler materials and fluxes. Advanced testing methods have been utilized for estimation of quality and characteristics of brazed joints.

Figure 1. SEM image (a) and EDS mapping results of TiC-430L high chromium steel cermets sintered at 1500 °C during 30 min (b): blue – titanium, red – chromium and green – iron.
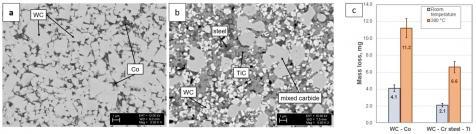
Figure 2 . SEM image of regular WC-Co hardmetal (a) and experimental WC hardmetal with high chromium steel (AISI430L) and titanium (b). Wear rate (mass loss) of hardmetals during erosion wear test at room and elevated temperatures (c).
Head of research:
Jakob Kübarsepp
jakob.kubarsepp@taltech.ee
With the development of rapid prototyping and rapid manufacturing technol- ogies the shape restrictions of manufactured parts have decreased gradually. One of the most promising near net shaping technologies is metal-based additive manufacturing by Selective Laser Melting (SLM), where functional metal parts with high accuracy can be obtained without any specific tooling. Topology optimisation by machine learning offers new possibilities for produc- ing components with lower weight together with lower amount of engineering hours spent for designing. Additive manufacturing enables manufacturing of these, usually organic shapes, for which traditional, subtractive methods cannot be used. An example of topology optimised part, used in formula racing car is shown in Fig.1.
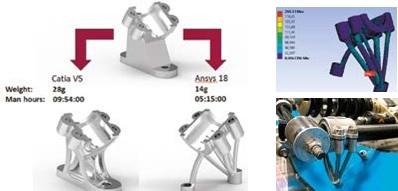
Fig. 1. Example of topology optimised and metal 3D printed part where both, weight at similar maximum stresses and man hours for designing could be drastically decreased.
The present research attempts to advance further in manufacturing of near net shaped parts by enabling tailoring material properties at selected areas of the part. This is realised through producing multimaterials. First, a porous preform is 3D printed which is followed by embedding with ceramic, metal or polymer through post treatments – infiltration or pressure assisted sin- tering. When combined with finite element analysis (FEA), the material in the part can be tailored to have specific properties in specific areas of the body (e.g. increased strength, hardness, wear resistance, chemical inertness etc.). Our investigations have shown that damage tolerance of highly brittle ceramics can be dramatically increased. For example, functional grading of ceramics – metal printed parts have high perspectives in orthopaedic appli- cations, where biocompatibility from ceramic and strength from metal can be adjusted in one part (see Fig.2).
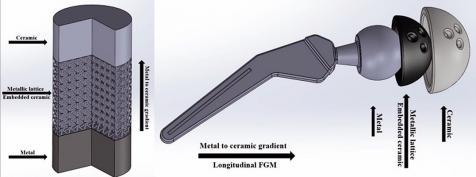
Fig. 2. Schematic of functionally graded metal-ceramic composite produced by SLM followed by hot isostatic pressing.
Interpenetrating phases in the composites allow retaining properties that are not seen in standard metal-ceramic composite. Additionally, non-compatible ceramics can be joined with metals. An example, where antimicrobial tita- nia-silver composite is bound to titanium alloy is shown in Fig. 3.
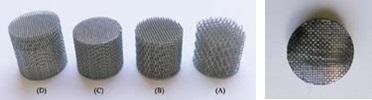
Fig. 3. Porous preforms manufactured by SLM and TiO2-Ag – Ti6Al4V interpenetrating phase composite manufactured by Spark Plasma Sintering.
In addition to revolutionising the complexity of the shape of elements that can be produced by additive manufacturing, the addition of ability to produce multimaterial near net shaped parts would open new industrial applications difficult to predict today. Our research is taking first steps in this direction by combining standard powder metallurgy and liquid metallurgy methods with selective laser melting..
Head of research group:
Lauri Kollo
lauri.kollo@taltech.ee
An important issue when evaluating road safety measures is assessment of indirect indicators of road safety. Here we focus the study on interac- tion between road accidents, traffic conflicts and road users’ behavior. Researchers have set a goal to understand what patterns in drivers’ and pedestrians’ behaviour lead to accidents and how it is possible to prevent them. The results of this work are addressed to designers of contempo- rary intelligent transportation systems and road infrastructure as well as to autonomous vehicles industry.
A traffic conflict is a traffic event involving an interaction of two or more road users, where an evasive action such as braking or swerving occurs to avoid a collision. Traffic conflicts are the surrogates of traffic accidents. These are more frequent events compared to accidents and provide a wider basis for research. Conflicts are registered with the help of contemporary semi-automatic video processing software, which was developed in partner universities (Lund University and Aalborg University). This software allows distinguishing of conflicts from other traffic events and describing them by means of special parameters (see Fig.1 – the parameter displayed is time to collision or TTC).
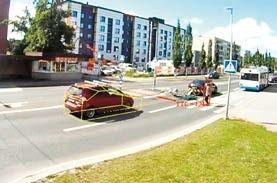
Fig. 1. Analysing traffic events in software T-Analyst.
Besides traffic conflicts researchers also study different aspects on road users’ behaviour. This is done to understand general trends and patterns in traffic behaviour. Respective knowledge is needed besides other things to describe the general background and to reveal the most actual problems in traffic behaviour that need to be dealt with. The latest project in this field was analysis of 16-year trends in road users’ behavior in Estonia (Ess J., Antov
D. 2017. Estonian traffic behaviour monitoring studies 2001–2016: overview and results. The Baltic Journal of Road and Bridge Engineering. Volume 12(3): 167–173).
Head of research group:
Dago Antov
dago.antov@taltech.ee
The progress in modern technologies and products combined with a growing energy demand and concerns about climate changes require development of new materials and processes that play a significant role in satisfying future needs of mankind. In this context, the ready availability of “tailored-to-use” structures appears to be the main issue that determines the speed of prog- ress. The development of innovative systems requires extensive research in order to design, develop and produce materials with increasing functional- ities and lifetime expectancy. Moreover, materials that can serve a variety of purposes are of special interest not only for a research community but also for demanding industrial applications.
The requirements for multifunctionality dictate accelerating interdisciplinary research activities in an emerging field, which incorporates mechanics, materials science, engineering science, physics, chemistry and biology.
The focus of our research is related to multifunctional hybrid materials mostly based on advanced ceramics. This direction is motivated by the fact that in many cases the development of top-end products has reached limits set by the limited capabilities of the currently existing materials, as well as by the urgent need in a knowledge-based design, development and processing of industrially applicable materials for energy technology, healthcare and transportation.
For example, ultralight and superelastic alumina ceramics are prepared by combining graphenated additives and alumina (see Fig. 1) to produce not only a relatively tough and strong, but also electrically conductive material meeting requirements often representing the trickiest trade-off between strength and toughness, electroconductivity and insulating behaviour.
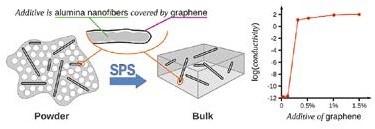
Fig. 1. A schematic representation of alumina-based composite of high electroconductivity and mechanical properties.
Introduction of spatial gradients also allows effective playing with mechanical and functional performance, and creating functionally graded materials of either isotropic or highly anisotropic properties. As an example, directional electro-conductivity combined with gradual change in hardness throughout the bulk is shown in recently developed zirconia/graphenated fibers composites, Fig.2.
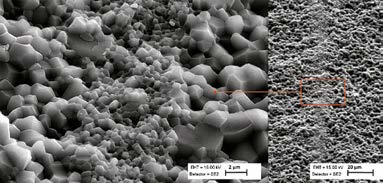
Fig. 2. Functionally graded zirconia of anisotropic conductivity.
On a more practical level, the group focuses on scalable spark plasma sintering and additive manufacturing of multi-functional structures, as well as controlling the microstructure design and macroscopic features to tune the material properties.
Our current top priority is powders for additive manufacturing through selective laser melting (SLM). In the field of polymers and metals, additive manufacturing methods are already established and used for manifold applications.
For ceramic materials, it is gaining more and more importance, especially as resource-efficient manufacturing method. Nevertheless, additive manufacturing methods for ceramics are at the beginning of technological development. The special attention is paid on the synthesis of powders converting ceramics and refractory metals of poor sinterability into materials of higher sinterability using chemical approaches developed by the team. Example is given in Fig.3..
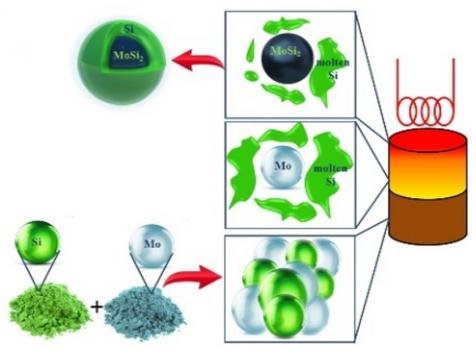
Fig.3. The schemaitc view of the combustion synthesis of MoSi2/Si core-shell particles for AM.
Head of research group:
Irina Hussainova
irina.hussainova@taltech.ee
Smart Composite Materials with Structural Health Monitoring Capabilities. A methodology for design of smart composites with the ability to sense and process information about the structural health and environmental conditions has been proposed. The monitoring is performed by use of sensor systems designed for particular composites structures (sensors may be embedded). Embedding a foreign structure inside a composite causes structural mis- match and integrity problems. At the same time it has many benefits, which makes embedding desirable for composites.
Smart composite materials and structures are developed based on use of novel additive layer manufacturing technologies (ALT). ALT is employed for producing variable geometry enclosures for the electronics. An embedded device with geometry which has minimal impact on stiffness and strength properties of host composite has been designed (see Fig.1). Combinations of the two ellipses with different half-axis are found to correspond to the optimal shape of an embedded device.
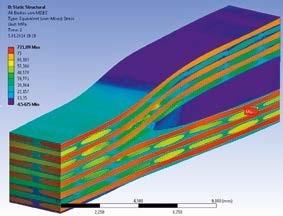
Fig. 1. Smart structure: stress distribution near embedded comp.
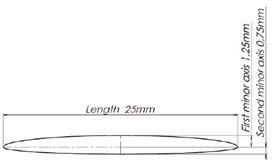
Fig. 2. Optimal shape of an embedded device: two half ellipses.
Design of Multifunctional Laminated Glass Structures. Main goal: an anal- ysis and design of multi-functional laminated glass composite panels with advanced sound and vibration attenuation properties, predefined stiffness/ strength properties and predefined transparency characteristics.
Elastic properties of the glass layer are determined from non-destructive acoustic tests. The Young modulus and Poisson ratio are computed based on measured values of the of P-wave and shear wave speeds. In the case of tempered glass the residual stress has significant impact on stress-strain behaviour. For that reason experimental study has been performed in order to determine residual stresses in glass layers. GlasStress SCALP-05 and the scattered light method were used to determine through-the-thickness stress distribution.
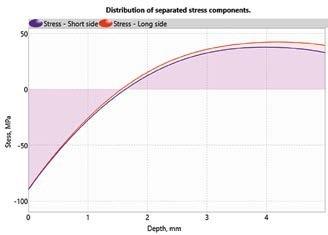
Fig. 3. Through thickness residual stress distribution in temp.glass.
Free vibration analysis of the laminated glass plate strip is performed by use of FEM analysis software ANSYSv16. A plate model for LGCP with advanced fractional Kelvin-Voigt viscoelastic interlayer has been developed.
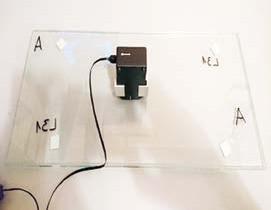
Fig. 4. Experimental setup. GlasStress SCALP-05
Head of research group:
Jüri Majak
juri.majak@taltech.ee
A loss due to wear of mechanical parts is estimated to be in the range 1.3‒1.6 % of a country's gross domestic product (GDP), therefore wear protection is crucible for improving the economical efficiency of a manufacturing process. Application of a hard wear resistant overlay (called hardfacing) to a metal surface by welding or thermal spraying is a widely acknowledged way to achieve this goal. In addition to that, hardfacings are also used for restoration of worn machine parts.
The research in TTÜ has been focused on composite hardfacings with a nickel- or iron-based matrix, reinforced by carbide (WC/W2C) and carbide-based (WC-Co, Cr3C2-Ni, TiC-NiMo) particles, for work under different wear types (abrasion, erosion, abrasive-impact wear) in a broad range of temperatures (20‒650 ºC). The main objective of the research has been to tailor the wear resistance of the hardfacings according to the working conditions and, on the other hand, to lower the final price. High velocity oxy-fuel spraying (HVOFS) and plasma transferred arc welding (PTAW) have been mostly applied as hardfacing technologies. HVOFS technology is principally used for hardfacings with thickness up to 1 mm and PTAW one – for hardfacings with thickness over 1 mm. The advantage of the HVOFS process is a much lower heat input to the substrate, what provides its lower distortion and neglidgible or absent loss of mechanical properties due to the annealing effect. In their turn, PTAW hardfacings demonstrate a much higher adhesion and resistance to impact loading, but the thermal input to the substrate is relatively high.
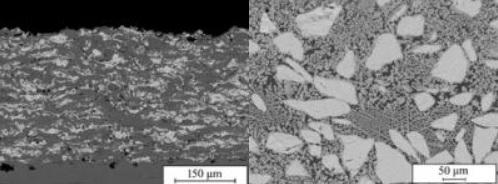
Fig 1. Left - Microstructure of WC-Co reinforced HVOFS hardfacing with FeCrSiB matrix. Right - microstructure of WC/W2C reinforced PTAW hardfacing with stainless steel matrix.
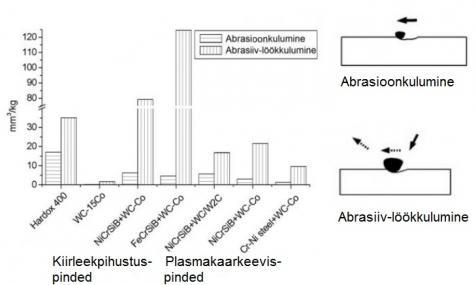
Fig 2. Left - comparison of wear rates of common wear resistant materials and composite hardfacings. Top right - scheme of the abrasive wear . Bottom right - scheme of abrasive-impact wear.
The hardfacings may be applied in highly abrasive conditions, occurring in mining, agriculture, etc. The concrete applications include pipe feeders, rippers, hammers, etc.
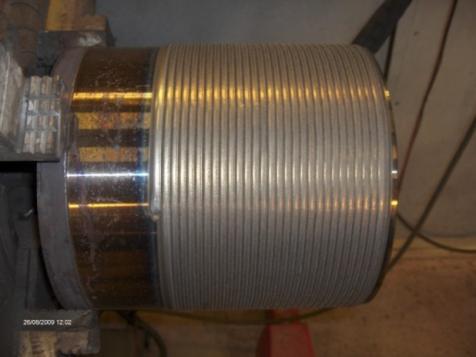
Fig 3. PTAW hardfaced riser pin (taken from TeroLink® by Castolin Eutectic®).
Head of research:
Priit Kulu / Andrei Surženkov
priit.kulu@taltech.ee / andrei.surzenkov@taltech.ee
Performance and service life prediction is an integral part of mechanical engineering and design of any part subjected to repeated loading during use. The goal is to accurately predict service life (or remaining service life) and increase the reliability of part functionality. This allows a company to have a competitive edge over its rivals in terms of optimised material selection and design considerations. In addition to machine parts service life prediction is relevant to other cyclically loaded structures such as overhead conductors and their fixtures, cutting elements of blanking dies etc.
The goals of the research are:
1. development of the product-based methods for evaluating their service life by using traditional or novel material testing methods.
2. clarifying of product-based failure causes and mechanisms and relate them to material microstructure/properties, including effect of residual stresses and design aspects.
The research is carried out in cooperation with Laboratory of Mechanical testing and Metrology. On one hand experts in the field of mechanical testing and accredited laboratory, with calibrated testing machines, on the other can work in unisom.
Areas of expertise:
• failure analysis, causes and measures to avoid failure,
• product development (material, heat treatment, production technology etc.),
• optimisation parameters of industrial production lines, laboratory and industrial tests with component control,
• material strengthening technologies (surfacing and heat treatment).
Area of applications:
• sheet-metal cutting and fine blanking
• assessment of automotive parts,
• assessment of aeronautical parts,
• energy transfer (overhead line conductors and fastenings).
Test and analysis methods:
• fatigue testing of metallic and non-metallic (hardmetals and ceramic) materials and coatings, including low and high temperatures,
• impact and fracture toughness testing, including low and high temperatures
• failure analysis and fractography (microstructure, composition, SEM, XRD and etc),
• quantitative and qualitative analysis methods,
• vibration testing.
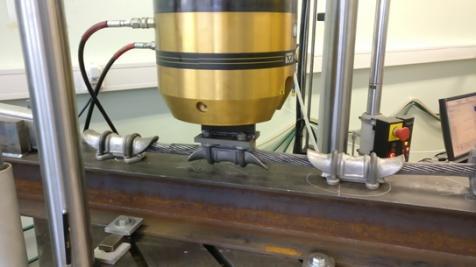
Fig. 1 Fatigue testing of overhead conductor.
Head of reasearch:
Mart Saarna / Priidu Peetsalu
mart.saarna@taltech.ee / priidu.peetsalu@taltech.ee
The Research Laboratory of Tribology and Materials Testing of TalTech is the only place in Estonia where materials can be tested under most of tribological working conditions present in real-life. The wear (loss or change of shape of the parts) cannot be excluded if the loaded parts are experiencing relative motion. So, actually, all parts of devices or equipment are suffering from wear or corrosion. The conditions that could be tested include sliding (with or without lubrication, at room or elevated temperature, etc.), abrasion (different loads, velocities, abrasive particles, etc.), erosion (dry or wet, different particle concentration, different temperatures, etc.), scratching, combined processes (tribo-corrosion, or impact-abrasion, for example). Please refer to Fig. 1 to get some hints on how the test method is selected.
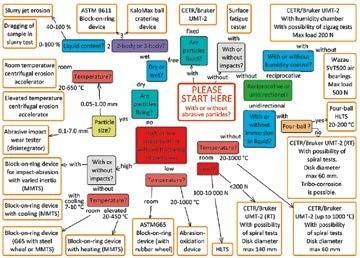
Fig. 1. The simplified scheme of tribological test method (available in the “Research Laboratory of Tribology and Materials Testing”) selection procedure.
We help companies to modify existing or to create new test methods to mimic real-life conditions (if they are not available yet). The Laboratory can do mechanical tests (compression, tension, bending, scratching, etc.) of small samples or soft materials (like paper or sponge, etc.) thanks to the presence of highly precise low-load sensors (load and position resolutions down to 0.5 mN and 1 µm respectively). Even the smallest wear of parts could be measured thanks to the 3D optical profiler with precision down to 0.01 nm. The Laboratory can provide the information to select the most appropriate material for your application. The tests can usually be done in one week´s time depending on the number of tests to be performed and availability of test equipment.
The Laboratory is working with Estonian as well as with international customers. We have contacts with other test laboratories around the world and we can help to find the suitable place for testing if it is available abroad. We regularly take part in high-level Estonian and European research projects aiming to increase the lifetime of key components influencing the reliability of equipment and safety of workers (please refer to www.nettun.org, for example).
The results of material testing can be used as an input to the continuous product improvement cycle to improve a material (or product) or to create a new innovative material (or product). The availability of the modern research, production equipment and modelling software allows designing, producing and testing of a new material in close cooperation with the employees of the Department of Mechanical and Industrial Engineering. The Fig. 2 shows the example of the novel 3D printed metallic material having extremely low coefficient of friction obtained even without the use of lubricants.
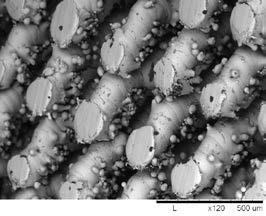
Fig. 2. The novel 3D printed (in Department of Mechanical and Industrial Engineering) metallic material having extremely low and stable coefficient of friction in dry sliding tests due to specific surface topography.
Head of research group:
Maksim Antonov
maksim.antonov@taltech.ee
Robotics is a rapidly developing area. Large companies as well as SME-s are installing new robot-based manufacturing systems to fulfil the basic demands for competitive manufacturing: high flexibility, low price of prod- ucts, guaranteed quality, and short throughput times. There is a need to find new ways to put the SME-s to develop their business and manufacturing to a new higher level. Today, we act in accordance with Industry 4.0 philoso- phy, which includes the following key points: Cyber Physical Systems (CPS), the Internet of Things (IoT), machine-machine intelligent interactions (M2M), wireless communication, reconfigurable engineering, etc.
Based on this a smart manufacturing model has been developed together (see Fig. 1) with the IMECC (Innovative Manufacturing Engineering Systems Competence Centre) and the development teams of TalTech Department of Mechanical and Industrial Engineering. The smart manufacturing model is the basis for different applications in companies.
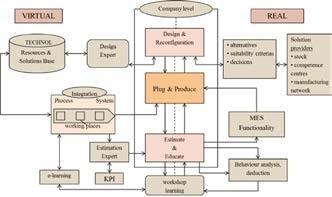
Fig. 1. Smart Manufacturing Based on Integrated Tools.
The main features of reconfigurable manufacturing are: distributed open architecture, interoperability of heterogeneous systems, clear layering and an interactive physical network; decentralized autonomic architectures based on intelligent decision making procedures; intelligence at the very edge of the networks, up to users’ terminals and things; cloud computing technology, event driven architectures, disconnected operations and synchronization; use to market mechanisms for increased competition and participation, including the possibilities of workplace off-line teaching, on-line monitoring, etc.
The model presented in Fig.1 is the basis for research projects and industrial applications, it also gives an input for different international proj- ects (Horizon 2020, i4MS, ERASMUS+, Interreg, etc.). One pillar in the new approach to manufacturing is a dynamic, reconfigurable modular production system, a fully-integrated, collaborative manufacturing system that responds in real time to meet changing demands and conditions in the factory and in the supply network. It is also necessary to investigate problems of self-moni- toring and self-healing capabilities of robot-based work-cells. On the basis of the smart manufacturing model different applications have been developed in the research centre IMECC. In Norcar BSB Eesti a use case has been devel- oped. The general objective is to develop a highly modular, multifunctional and adaptable smart factory system platform with robot cells that provides a complete solution for reconfigurable manufacturing with an aim to provide flexibility, shorten order fulfilment cycle time, reduce costs, raise resource efficiency and develop a new business model (see Fig.2).
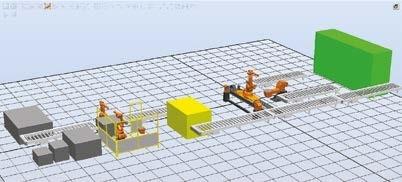
Fig. 2. Developing smart robot based system for welding parts with lot size 1.
In a new robot cell development process an integrated solution to control automated stock with RFID solution for cartridges and machine vision sys- tem for product recognition is needed. The cell has to be integrated with all production system components (Robot Studio, ERP, MES, etc.).
Nowadays production systems are quite sophisticated and there is a need for integrated knowledge and skills. For better education and for organizing adult training courses but also for experimental work the FMS and Robotics Demo Centre has been established on the premises of TalTech Department of Mechanical and Industrial Engineering.
TalTech and IMECC are partners also in a Digital Innovation Hub (i4MS proj- ect). The Digital Innovation Hub (SmartIC-Robotics) is a structure, collaborative working place for networking and supporting the companies, especially SMEs in introducing new digital technologies for increasing their competitiveness.
Head of research group:
Jüri Riives
juri.riives@taltech.ee
The main objective of the investigations is to develop highly effective and high-tech acoustic materials for a wide field of applications. Traditional porous materials (wool, textile, organic absorbers can deteriorate over time, pollute the surrounding medium by radiating small particles and be poten- tially harmful. Solid fibreless micro-structured materials, such as micro-per- forated panels (MPP), micro-grooved elements (MGE), metal foams and acoustic meta-materials (AMM) are expected to become a good replace- ment to the conventional absorbers in noise control. However, the physical mechanism behind the new sound absorption materials needs to be further investigated and optimized.
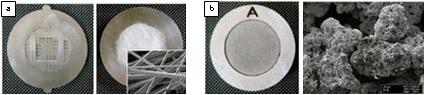
Fig. 1. Photo of the Micro-grooved element and of traditional glass fiber wool (a) and sintered metal powder sample and magnification 50X (b).
MPP absorbers consist of thin metal plates with holes less than 1 mm in diameter. Sound attenuation of the plates can therefore be accomplished without exposing humans to potentially dangerous airborne fiber particles. Panels can be manufactured from materials that have high fire rating (i.e., not flammable or smoke generating).
Another class of material which has been investigated is represented by the acoustic meta-materials. AMM, typically based on the inclusion of small, periodically spaced in-homogeneities, have high potential in noise control and show effective macroscopic acoustic behaviour. It can be, for instance, a composite containing microstructural element comprising heavy masses surrounded by a soft elastic material annulus arranged periodically in a three-dimensional solid matrix. Also ducted structures with tensioned membranes, behaving as moving mass, have been investigated. Carefully designed and optimized periodic structures, located along the waveguide of one dimensional propagating wave, also act as meta-material structure and enable achievement of considerable sound attenuation.
Negative compressibility, which is necessary for acoustic meta-materials, can also be realized with the well-known acoustical element, the Helmholtz resonator, above its resonance frequency where the cavity volume acts as a dynamic volume source. Therefore, a useful example of meta-structure is represented by a periodic resonator matrix added to the flow duct.
Considering the even sometimes complicated structure of the micro-struc- tured acoustic materials, new material-additive production technologies open a wide perspective to create solid acoustic materials for any specific application. In order to considerably reduce time needed for experimental investi- gations of the acoustic materials, new measurement techniques based on transfer functions and simultaneous analysis of acoustic signals, are devel- oped. The developed methods, together with the dedicated measurement rig, enable determination of the acoustic and flow dynamic parameters at both high temperatures and high flow speeds.
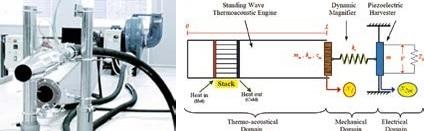
Fig. 2. Test rig to determine acoustic parameters of micro-structured materials at high flow speed and high temperature (a) and Schematic of acoustical to mechanical power conversion and final energy harvesting (b).
Vibration-based energy harvesting, the scavenging of power from existing vibro-acoustic source and its conversion to useful electrical power, is becom- ing important. The design of energy harvesting devices must be optimized to produce the maximum output for given ambient conditions.
The vibro-acoustic non-linear behaviour of membranes and thin films has been shown to be significant for both harvesting and damping of acous- tic power, thus their influence on the system performance is systematically investigated.
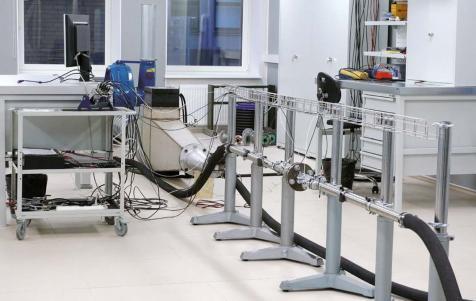
Head of research group:
Jüri Lavrentjev
juri.lavrentjev@taltech.ee
In a broad sense, coatings and films technology is a very important branch of science and industry. Development of coatings and films technology toward their functionality has been attracting much interest. Innovative coatings and films can be characterized as materials with special properties tuned for specific applications. Research and development of modern materials are substantially based on hybrid materials technology. Hybrid structures can consist of different materials (metals, ceramic, etc.) in different forms (bulk, layered, composites, gradient structures, etc.) in nano, micro, and macro level.
The research group in TalTech deals with all aspects of physical vapour deposition (PVD) and chemical vapor deposition (CVD) technologies. The advanced diamond (see Fig. 1) and oxide coatings are under development. The coatings characterization includes investigation of tribological properties (room/high temperatures), mechanical properties by nanoindentation and nanoscratch (room/high temperatures), surface morphology and chemical composition, etc. Diamond coatings (see Fig. 1) have a wide range of tribological applications due to high Young’s modulus and hardness. Different types of coatings are used for protection of cutting tools in engineering and mining industry. High temperature wear resistance is important for cutting tools. Therefore, the study of tribological behaviour of diamond coatings at high temperatures is of special interest. Investigation and improvement of diamond coating properties, particularly the properties of the interface between the coating
and substrate is an important part of the current research.
In regard to oxide coatings, understanding and improvement of thermal resistance of the AlCr-based oxides is the specific research topic. There is a need for the development of new coatings for cutting tools used in modern machining processes.
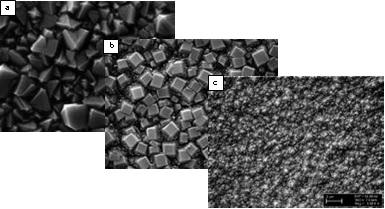
Fig. 1. Two types of diamond coatings, polycrystalline (a,b) and nanocrystalline (c).
Extreme high temperature conditions occur during metal cutting processes suggesting to use coatings with special properties. One major role of the coatings for this type of application is to prevent surface oxidation and alternation of properties of the tools at high temperature. The selection of coatings is restricted to materials with phase stability and low wear rate at high temperatures, resistance against oxidation, low thermal conductivity, chemical inertness, appropriate thermal expansion coefficient, etc. Measurement of thermal expansion coefficient is another important aspect, as this coefficient characterizes an ability of a material to withstand the thermal stresses associated with heating and cooling. The project focuses also on the understanding of influence of the structure of oxides (chemical composition, type of phase, impurities, micro/macro defects, etc.) on the thermal and mechanical/tribological properties of oxides.
Applied study focuses improvement of wear resistance of tools by applying high-technological thin hard PVD coatings for specific tooling applications (fine blanking and sheet metal forming dies, cutting tools etc.).
Head of research group:
Vitali Podgurski
vitali.podgurski@taltech.ee